Sigrest Research Cont’d
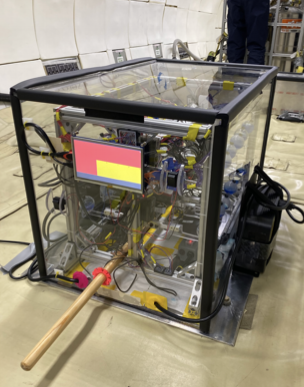
Tell us about your first parabolic flight and what experiment did you do?
On my first parabolic flight I experimented with a novel microgravity slosh mitigation technique. This is the research with which I qualified for ISEF this past year. The day before the flight, I conducted a test readiness review with the Zero-G Corporation. Then, I mounted my test apparatus into the plane and powered up the whole experiment to conduct an electromagnetic interference test. On the day of the flight, there was an ID check, then we loaded onto the plane. During the flight, there were 4 “calls”. “On the pull” is a 2-g climb towards the top of the parabolic arc. “Pushing over” is the plane transitioning at the top of the parabolic arc. “Release” is called when the plane achieves microgravity. And “Feet down, coming out” means the plane is exiting microgravity. Once the “Release” call was made, I would wait 5 seconds, then initiate an acceleration to the test apparatus using my push rod. The motion caused the fluid (aka water because hydrazine is extremely dangerous and difficult for a high schooler to get her hands on) to slosh, or move, around inside the tanks. Using Raspberry Pi’s and Pi Camera’s I recorded the sloshing of the tanks to review later. I also used hand-held GoPros as a redundant video collection system.
My experiment tested the ability of custom surface energies to reduce the settling time of fluid and increase the fluid aggregation around a fluid sump. Settling time is the time it takes for a fluid to stop moving after being disturbed by an acceleration. The fluid sump is where the fluid is pulled into the engine (it is easiest to think about it as the bottom of the tank). And fluid aggregation means where the fluid collects or “pools” together.
Tell us more about your slosh and your experiment.
Slosh is unwanted movement of fluid in a tank and has caused many failed space missions. Slosh occurs during spacecraft launch and in microgravity during maneuvers. NASA and spacecraft developers have spent billions managing slosh. Baffles effectively manage launch slosh; however, mitigating slosh in microgravity, in which surface energies rule the fluid dynamics regime, requires costly subsystems that add weight and complexity. My ISEF project describes a novel method to manage microgravity slosh through custom surface energies.
Spherical acrylic tanks were treated with superhydrophobic and superhydrophilic coatings and filled at various fill fractions. The settling time for the “fluid” in coated tanks was compared to non-coated (control) tanks after an imposed acceleration. Additionally, fluid aggregation around the sump was compared between coated and non-coated tanks. The experiment was replicated for tanks with simulated propellant management devices (PMD’s). Microgravity was achieved through G-FORCE ONE weightless lab operated by Zero-G corporation.
This experiment supported the hypotheses with a significant reduction in settling time for coated tanks. Settling time reductions of 73% for high fill fractions and 59% for low fill fractions were achieved. The coated tanks aggregated the liquid at the sump 100% of the time, compared to 12% for the control tanks without PMDs and 64% for control tanks with PMDs. The results demonstrate a method to eliminate slosh subsystems, reducing cost, weight and complexity and increasing mission reliability and capacity. A continuation experiment will be flown on an upcoming sub-orbital flight of Blue Origin’s New Shepard Rocket with the purpose of validating parabolic-flight results and collecting slosh-induced forces in extended microgravity. The experiment may also be expanded from spherical to conformal tanks. There is a patent pending on my method.